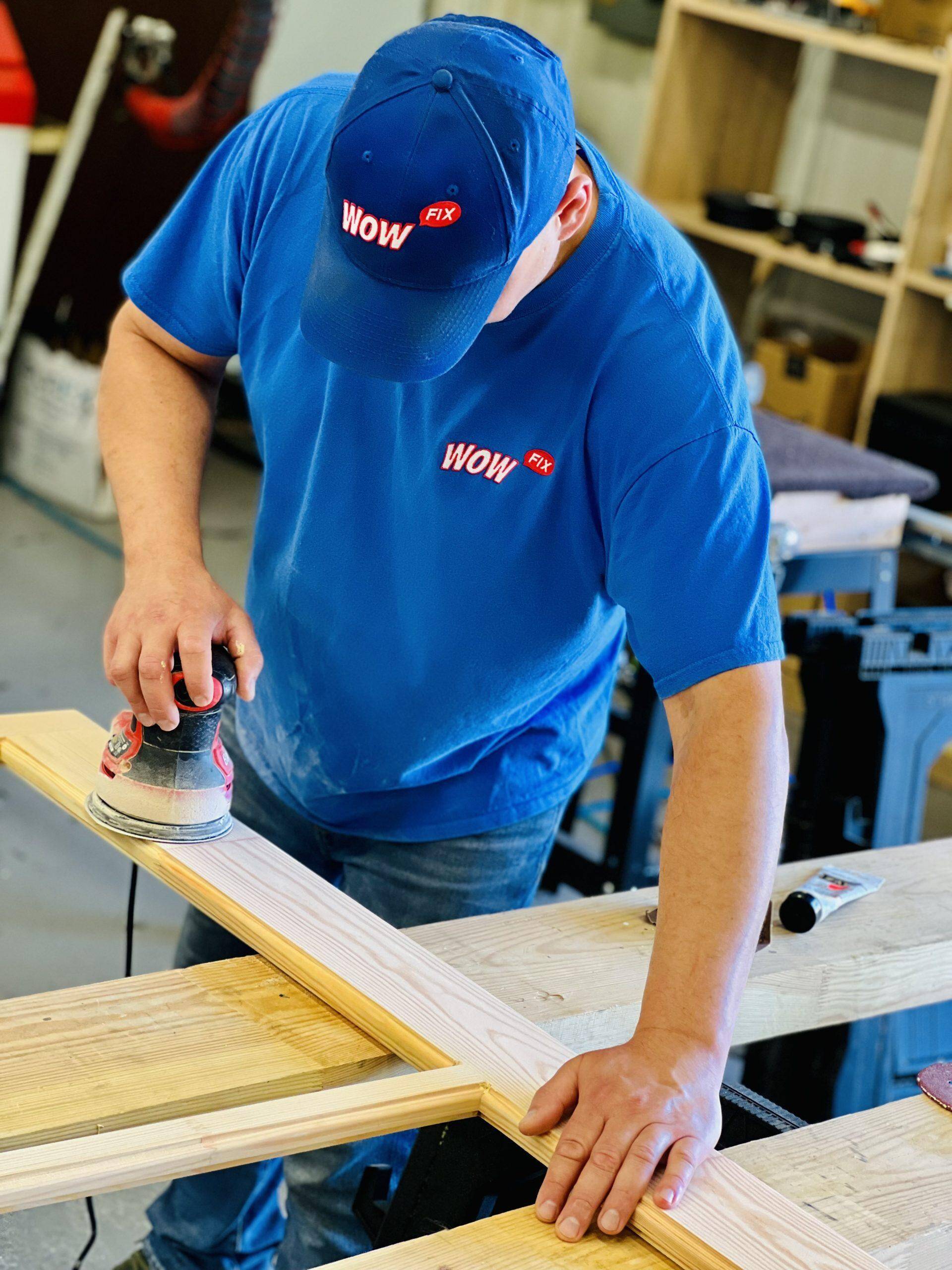
Metal Fabrication Services
Where precision meets perfection in metal fabrication. Elevate your projects with expert craftsmanship and cutting-edge technology. Unleash excellence, choose WowFix!
WOWFIX INTRODUCTION OF METAL FABRICATION SERVICES:
Wowfix sets the gold standard in metal fabrication with over 15 years of experience providing top-tier solutions across industries. Our state-of-the-art facility is equipped for complex, customized projects, combining advanced machinery with skilled engineers and metalworkers.
We offer a comprehensive range of services including CNC laser cutting, all Possible and impossible Welding, machining, finishing, affordable window repair and powder coating—all under one roof. With technical precision and creative problem-solving, Wowfix produces metal components tailored to meet your exact specifications and quality standards.
As a trusted name in metal fabrication for over a decade, we partner with customers to ensure complete satisfaction from start to finish. Contact us today to learn more about our capabilities and why the top companies continue to choose Wowfix for replacement windows.
or Request Call Back
WOWFIX expert engineers provide accurate quotes for any size project.
Below is some of our services introduced:
If you don’t see your Custom Metal fabrication need, please do not hesitate to call us for FREE consultation.
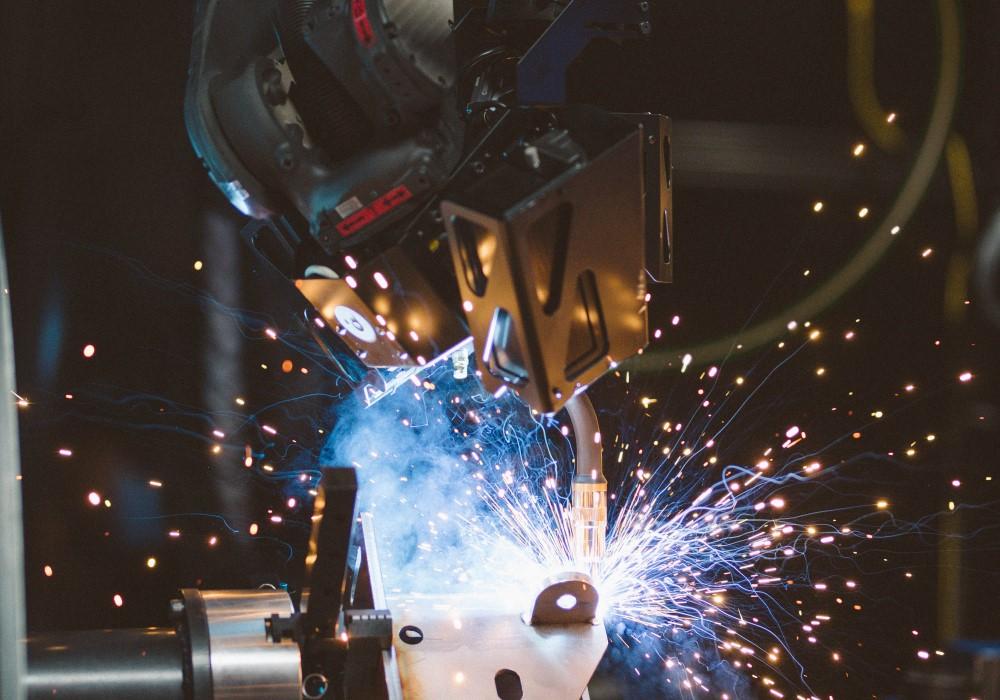
Robotic Welding
CNC Laser Cutting
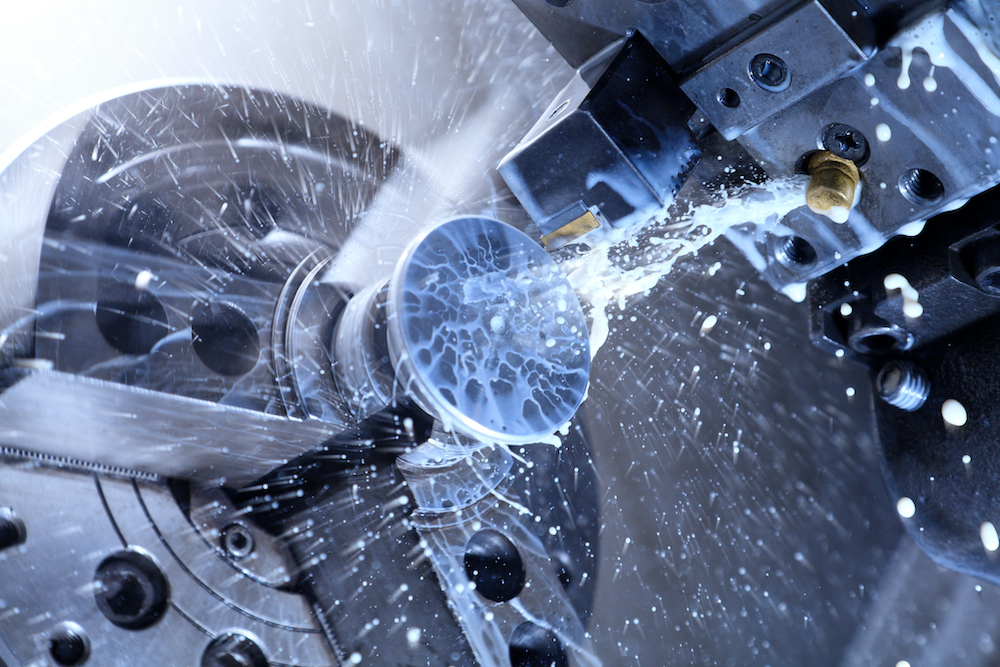
CNC Lathe Machining
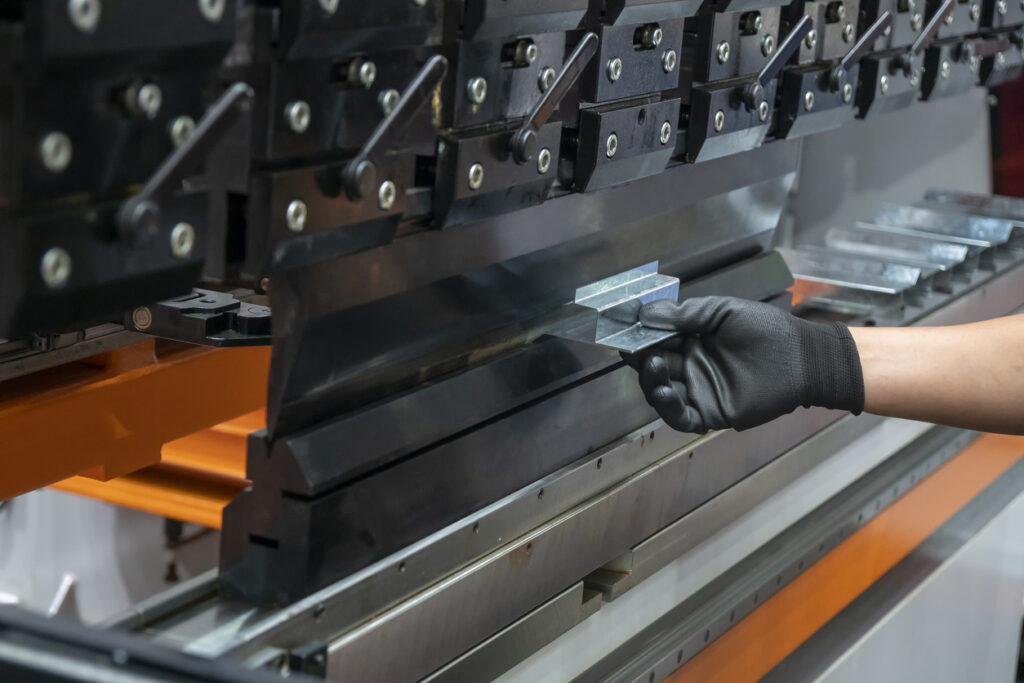
Metal Forming
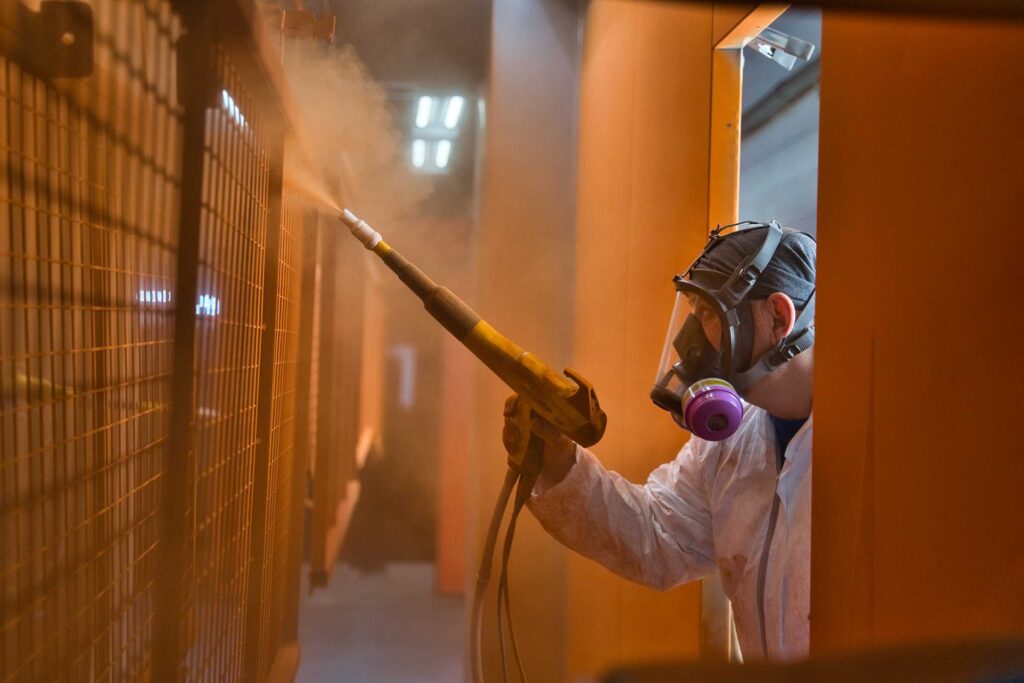
Powder Coating
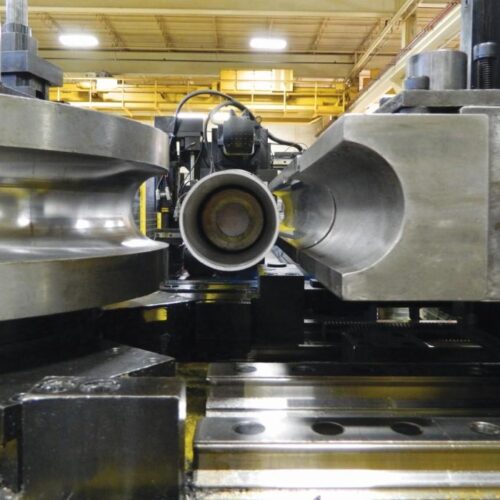
3D CNC Pipe Bending
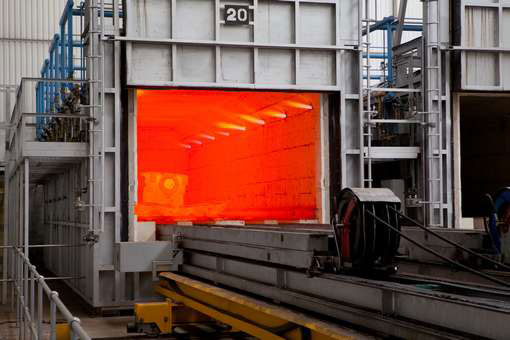
Heat Treating
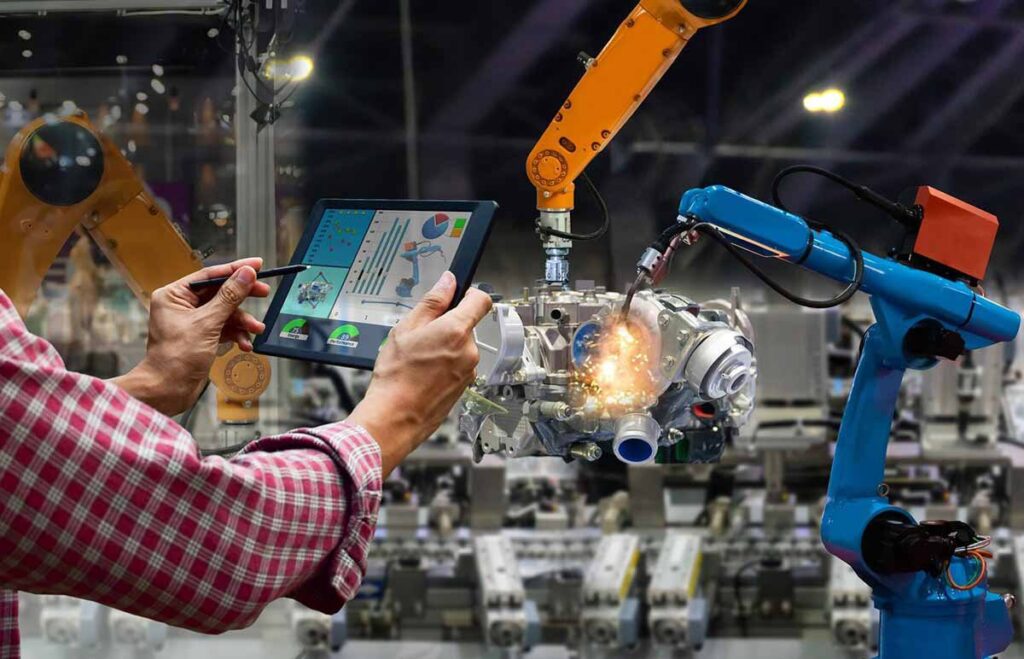
Industrial Automation
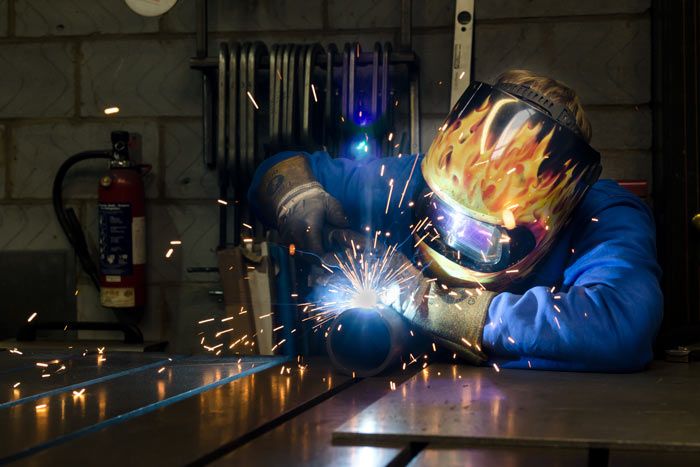
Industrial Welding
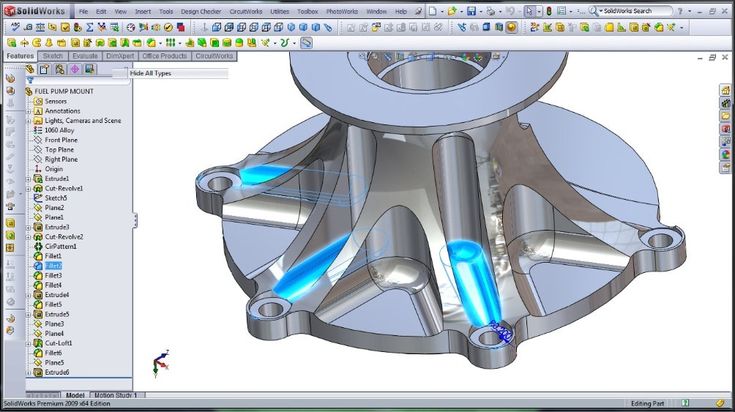
Prototyping
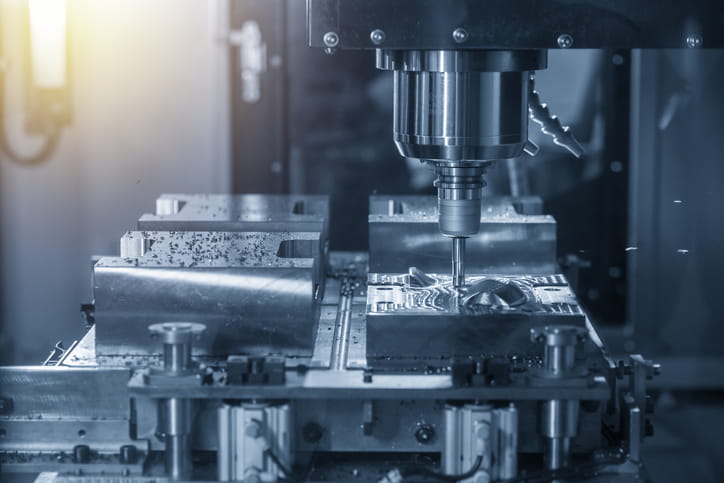
CNC Milling
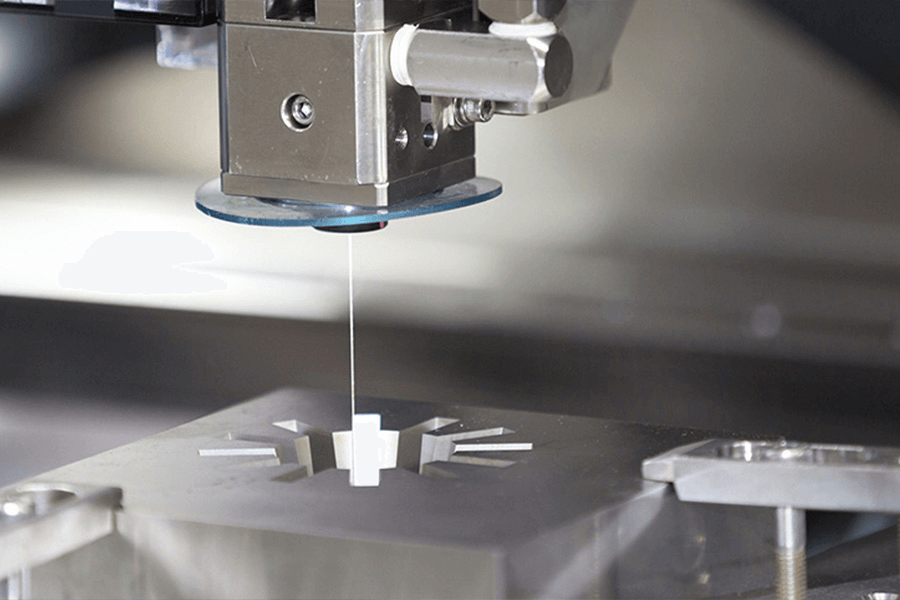
Wire EDM Cutting
Unparalleled Metal Fabrication and Machining Solutions
For over 15 years, our state-of-the-art manufacturing facility has been providing best-in-class fabrication and machining solutions for customers across industries. We offer an incredibly comprehensive range of services including broken window repair that enable us to provide virtually any custom metal component required. From simple brackets to complex assemblies, prototypes to high-volume production runs, our capabilities facilitate bringing client ideas to reality quickly and cost-effectively.
Advanced Cutting and Machining Capabilities
At the core of our manufacturing services is an array of precision cutting and machining capabilities able to meet even the tightest tolerances and most demanding project requirements.
Our CNC milling and turning machinery is expertly programmed and operated to deliver exceptionally repeatable results regardless of order size. Configured with live tooling, Y-axis capabilities, and driven by the latest controls, our HAAS machining centers rapidly transform blocks of aluminum, steel, titanium, plastics and other exotic alloys into high precision components.
Complementing our milling capabilities, our precision CNC lathes, backed by ongoing operator training, provide accurate, efficient production of turned parts from single pieces to thousands. In conjunction with CNC milling, complex components requiring multi-process machining are handled with ease.
And for complexity beyond standard CNC machining, our state-of-the-art EDM and laser cutting afford additional advantages:
Wire EDM Cutting: Our reliable wire and sinker EDM equipment affords very accurate machining where traditional methods fail – especially useful for hard or high-strength materials. The spark erosion process eliminates burrs while achieving tolerances down to 0.0001 inches even when producing small openings or cavities. Graphite electrodes custom machined on our mills are used for shapes difficult or impossible to produce otherwise.
Laser Cutting: Our high-powered lasers produce extremely clean cuts in sheet metal while maintaining exceptional edge quality. Tight positioning accuracy allows creating intricate cut patterns and small openings. We readily laser cut steel, stainless steel, aluminum, copper, brass and more up to 0.750 inch thickness.
Automated Robotic Welding Solutions
Robot welding systems have transformed manufacturing enabling extremely fast production. Our state-of-the-art KUKA arc welding robots optimize throughput while minimizing human effort. For companies with high-mix low-volume production, the automation flexibility allows quick changeover between various products. Whereas, high-volume runs achieve unparalleled consistency with 24/7 operation.
Our welding engineers program the optimal motions to suit part geometries and specifications. Fixturing and indexing equipment is custom fabricated in our machine shop allowing flexible automation. The consistent high-quality robot welding significantly minimizes secondary clean up operations. And versus manual methods, the reliability enhances control over every parameter critical to quality.
For industries with strict welding procedure specifications, our cross-trained robotic technicians ensure stringent in-process monitoring. This includes thermal regulation critical for materials like aluminum and stainless steel. Components also undergo non-destructive examination such as visual inspection or liquid penetrate testing based on client requirements.
Metal Forming and Fabrication
Achieving final part geometries may require additional forming or fabricating processes prior to or following CNC machining and robotic welding steps. Our extensive range of metal forming machinery provides flexible options for prototype through production scale fabrication.
Press Brake Forming – Our Amada press brakes, together with precision tooling provide exceptional control over bend angles and edge finish. By exerting hundreds of tons of pressure, we routinely form complex brackets, enclosures, frames and more from aluminum, carbon steel, stainless and other metals up to 0.5 inches thickness.
Punch and Shear – Our state-of-the-art punch presses quickly create holes or shear edges with CNC programmability to form parts from flat stock metal with incredibly repeatable accuracy. Combined with our Amada press brake forming, we efficiently handle high production fabrication orders.
Annotation welding fixtures: To facilitate robotic welding, custom fixtures made in-house securely locate metal fabrications ensuring quick loading repeatability. Backed by inspection reports, our machined weldments meet the most stringent tolerance requirements.
Throughout the fabrication process, quality control procedures ensure consistence and reliability. Additional value-added services like silkscreen and laser marking can be integrated according to client branding needs prior to final shipment.
Surface Treatments and Finishing
For enhancing durability or aesthetics, we offer various surface treatments:
Powder Coating: Ideal for improving appearance and preventing corrosion, our modern powder coating lines apply specialized formulations based on temperature resilience, gloss levels, colors and textures per specification. Compared to paint, powder coats emit near-zero VOC, entirely eliminating liquid waste streams. Preparation includes multistage wash systems while flexible batch coating facilitates protoypes through production orders.
Plating: Electroplating treatments enhance hardness, wear and corrosion resistance of machined components. Commonly specified finishes like zinc, nickel, chrome and cadmium are routinely applied to small and high volume production runs per QQ and AMS plating specifications.
Heat Treating: To modify the microstructure and significantly strengthen machined metal parts, various program controlled heat treating processes are offered including annealing, hardening and tempering. Process validation protocols ensure uniformity and consistency when treating high volume orders.
Industrial Automation Solutions
Transitioning suitable manufacturing operations from manual labor to turnkey automation continues an upward trend delivering transformative productivity, quality, and safety benefits. Our extensive expertise ranges from developing standalone machines to fully custom robotic welding and assembly cells seamlessly integrated with supplier components or legacy equipment.
Automated Equipment: Where feasible, converting manual or unreliable equipment to programmable CNC motion affords marked improvements in output, precision, and changeover times. Our self-contained automation utilizes industrial-grade electrical cabinets, pneumatics, servo-drives, PLC control, and operator interfaces purpose built for harsh production environments. Safety is paramount with UL-listed control panels, E-Stop circuits, guarding and compliance with other relevant directives.
Robotic Workcells: By programming optimal motion sequences, robotic arms excel at repetitive tasks like material transfer, inspection, welding, grinding, material removal and product testing. We design and build custom end-effectors, feeders and fixtures tailored to handle customer parts reliably and accurately. For process validation, data from vision systems, test instrumentation, torque tools and other sensors is collected and trended automatically. By seamlessly offloading tasks better suited for automation, our cells amplify human capabilities multifold.
Production Line Builds: To multiply productivity further, we integrate cells together creating customized production lines dealing with everything from component staging, processing, validation and packaging. Production data, OEE metrics and real-time notifications are displayed on HMI screens while gathered centrally for optimizing line efficiency. As products change over time, modular designs allow easy reconfiguration, upgrades or substitutions.
Prototyping Services
Bringing ideas to market faster provides game-changing business advantages. Our full suite of in-house capabilities enables rapid prototyping of customer designs to examine form, fit and functionality before committing to tools or large production runs.
We collaborate with clients starting from napkin sketches or concept CAD models. Our engineering team provides design-for-manufacturing expertise guiding CAD models suitable for production. Leveraging our manual and CNC equipment, early-stage metal and plastic prototypes are fabricated allowing customers to perfect designs through iterative hands-on testing.
When ready for validation prototypes prior to market launch, our capabilities produce models indistinguishable from finished goods. Prototypes contain the same specified materials, treatments and processes identical to subsequent production runs. In essence, our manufacturing technology facilitates compressed product development timelines saving customers tremendous time and expense during this critical phase.
In Summary
Our passion for innovation and delivering manufacturing excellence has earned us longstanding partnerships across diverse industries. For highly complex or incredibly straightforward parts, we have demonstrated success time and again. Our customer-focused approach ensures open communication every step of the way leading to the exact solution envisioned. We invite you to engage our team with your specific project needs and discover firsthand why clients continue choosing us year after year.
FAQ About Our Metal Fabrication Services
- We work with all common metals and plastics including steel, aluminum, stainless steel, copper, brass, plastics like ABS and nylon, etc. Our range spans from basic raw materials to finished castings and extrusions.
- Our 60,000 sq ft shop is fully equipped with latest CNC mills, lathes, press brakes, shears, lasers, EDMs, robotic welding cells, powder coating lines, etc. This allows us to deliver complete parts without relying on outside vendors.
- Absolutely. We build functional prototypes for concept validation, iteration testing, design verification and pilot production. Both metal and plastic parts can be rapidly fabricated using our in-house manual and CNC equipment.
- We fulfil both prototyping quantities in the 1-10 range along with high-volume orders of 10,000+. For large orders, our robotic welding cells ensure reliable, consistent output around the clock.
Yes. Apart from machining and fabrication we provide various finishing processes:
- Powder coating
- Wet spray painting
- Silk screening for branding
- Heat treating like hardening or annealing
- Plating like zinc, nickel, chrome, etc.
Connecting with our engineering team early when evaluating options is best. We can provide DFM analysis for your models to offer cost-effective solutions tailored to your needs - whether new product launch or existing line optimization.
Our expertise serves clients across medical, robotics, industrial machinery, transportation, energy and more. With tight quality controls we consistently meet the stringent requirements prevalent in regulated sectors.
Please reach out with any additional questions! We look forward to earning your business.